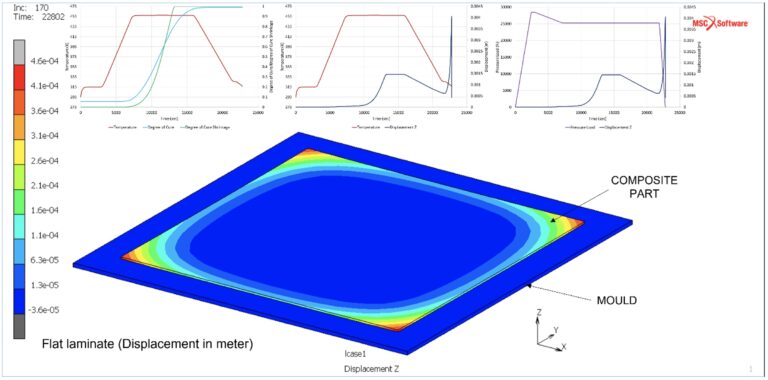
High-performance computing (HPC) enables companies operating in any industrial sector to become more innovative, more productive and maintain a competitive edge. But above all, with the help of cutting-edge technologies such as cloud supercomputing, artificial intelligence, machine learning and big data analysis, companies can develop products and services with a higher added value.
Among some others industrial sectors, EXCELLERAT partners support also the Aerospace industry with services and expertise.
The aerospace industry can greatly benefit from using HPC and Artificial Intelligence technologies. Those technologies and significant computational power are crucial in the aerospace industry for several purposes. HPC enables complex simulations and modeling of aerodynamics, structural mechanics, and fluid dynamics. It allows aerospace engineers to perform detailed analyses of aircraft performance, including airflow patterns, stress distribution, and fuel efficiency. AI can enhance these simulations by enabling optimization algorithms and machine learning techniques to improve designs and performance.
Furthermore, HPC and AI enable engineers to explore a wide range of design options quickly and efficiently. By leveraging computational power and AI algorithms, aerospace companies can optimize aircraft components, structures, and systems to enhance performance, reduce weight, improve fuel efficiency, and minimize environmental impact.
AI plays a crucial role in developing autonomous systems for the aerospace industry. It enables intelligent decision-making, real-time data processing, and sensor fusion for autonomous drones, satellites, and unmanned aerial vehicles (UAVs). HPC supports the complex computations required for autonomous navigation, object detection, and mission planning.
When coming to the Data Analysis and Predictive Maintenance, the HPC comes in very handy. The aerospace industry generates vast amounts of data from sensors, aircraft systems, and maintenance records. HPC and AI can process and analyse this data to extract valuable insights, detect patterns, and predict maintenance needs. This predictive maintenance approach helps reduce downtime, increase safety, and optimize maintenance schedules.
Lastly, HPC and AI technologies can improve aerospace manufacturing processes. AI-powered computer vision systems can detect defects in aircraft components, reducing the need for manual inspection. HPC enables advanced simulations for additive manufacturing, composite materials, and optimization of manufacturing processes.
FF4EuroHPC is an H2020 R&D project which promotes using HPC and complementary technologies such as HPDA and AI. Two Open Calls were offered through the project, targeting the highest quality experiments involving innovative, agile SMEs from varied application domains. SMEs were part of the experiments, that met the Open Call standards and have been carried out on the Cloud-based HPC systems. The experiment is an end-user-relevant case study demonstrating the use of Cloud-based HPC and the benefits it brings to the value chain from the end-user to the HPC-infrastructure provider thus must address SME business challenges by using HPC and complementary technologies such as HPDA and AI. When the experiment is successfully concluded, it is resulting in a success story, inspiring the Industrial community.
One of the success stories is briefly presented in this article. Please find more success stories on the FF4EuroHPC website.
Aeronautics: Multiphysics and Multiscale Modelling of Aeronautical Components
The autoclave moulding process – where composite layers are placed on a mould based on a lamination sequence and cured inside an autoclave using a vacuum, heat, and pressure – is the main fabrication method for composites used in the aerospace field. This process involves both mechanical and chemical phenomena, and a correspondingly high number of variables affect the final result.
Working with innovative materials and geometries leads to an increased number of defects and voids in the finished components which then are rejected. During the curing process, the mechanical stresses in the various materials rise, and this can lead to undesirable consequences.
Given the expense of the autoclave process, it is important to minimize defects in the finished components.
Currently, an expensive trial-and-error approach is used to find the optimal process parameters to produce complex-shaped components while minimizing the risk of voids or geometric distortions. This leads to long development times and high costs.
Manta Group’s aim is a more effective manufacturing process for its products: finding the optimal process parameters by multi-scale and multi-physics numerical simulations. This significantly reduces the necessary development times and costs as compared to the currently used trial-and-error approach.
Building multi-scale numerical models by employing HPC resources
To optimize the autoclave process parameters (e.g. the lamination sequence, the maximum temperature, the cure times, the times of heating, the maximum pressure), the different phenomena during the curing process need to be simulated to predict the parameters’ effects on the quality of the components to be manufactured. To this end, two separate multi-physics and multi-scale numerical models were set up, employing HPC resources. In detail, these are (a) a thermo-mechanical model (on the macro scale) to predict the dimensional variations of the laminates due to the residual stresses generated during the autoclave process, and (b) a fluid-structure model (on the micro-scale) to simulate the resin flow during the pressure application. Both numerical models were validated by comparison with results of experimental tests. To reduce the computing times, the use of HPC resources and the scalability of the simulations were analysed substantially.
Thermo-mechanical model (on the macro-scale)
The aim was to investigate the dimensional changes of flat and L-shaped profiles due to the residual stresses generated during the curing process. The technological process used to manufacture these profiles was the vacuum bagging. A Finite Element numerical model was implemented to simulate the curing process, subsequently validated through experimental tests.
To exhaustively simulate the manufacturing processes of composite materials, various phenomena that take place during the curing process, such as thermal flows and cure kinetics, were considered as they lead to macroscopic defects.
The curing process is modelled through a thermo-mechanical approach, that concerns the cure phase and the residual stress analysis. In this stage, the heat transfer and the curing influence the stresses and, consequently, the deformations of the part. The material is treated as a composite and the temperature and pressure cycles are simulated with the relative effects on shrinkage and spring-in.
Figure 1 shows the contour plot of the dimensional changes of the flat laminate during the autoclave process. As the temperature increases the strength and the mechanical properties of the composite material increase due to the resin polymerization. Moreover, the chemical transformation of the resin generates tension stress for the chemical shrinkage. During the cooling phase, residual stresses rise due to the CTE mismatch of fibres, matrix and mould material. The residual stresses result in undesirable dimensional changes during the demoulding. The geometric distortions after curing are about 0,5 mm along the axis Z.
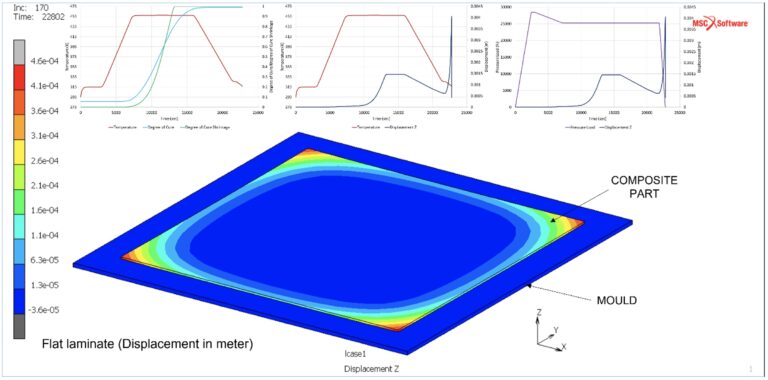
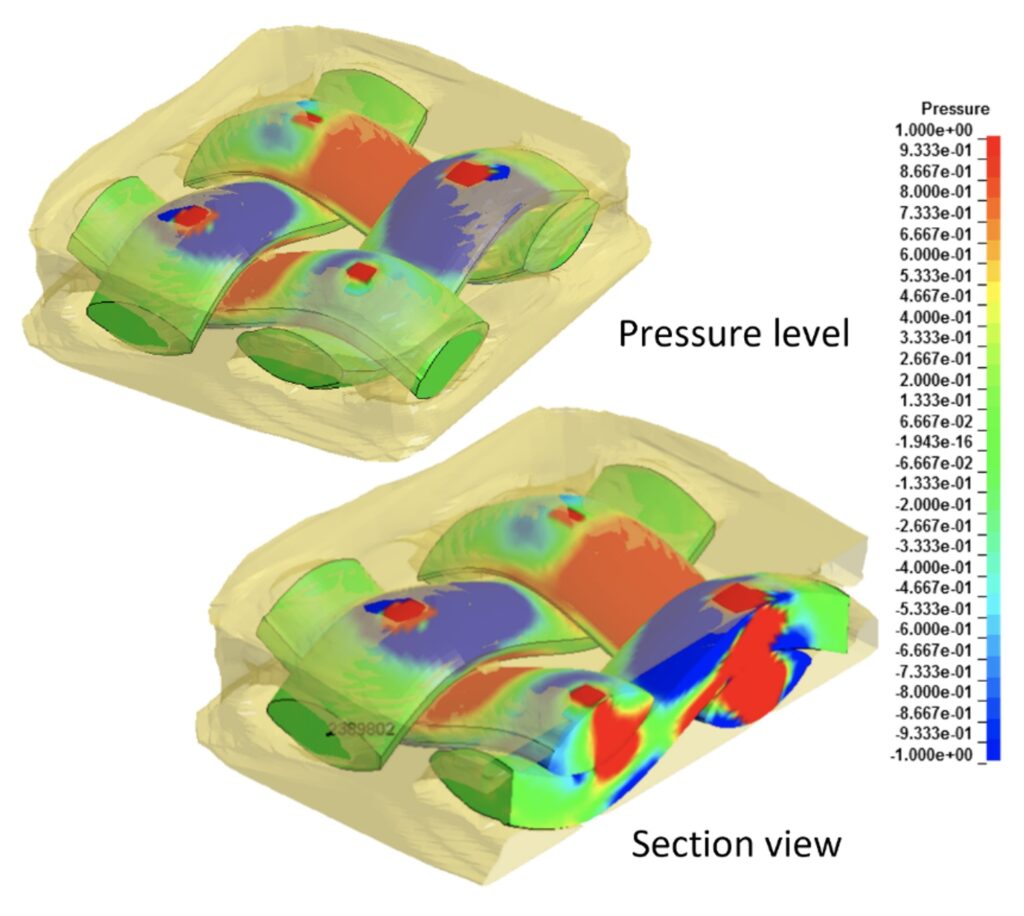
Fluid-structure model (on the micro-scale)
To simulate the pressure effects a fluid-structure model on a micro-scale level was implemented. The finite element model generated at the micro-scale allowed to carry out simulations regarding the pressure effect of the resin flow on the defined fibres layup, see Figure 2. The optimal pressure value for the process is close to 0,6 MPa (6 bar) and represents an acceptable compromise among the integrity of tows, the level of voids, the compaction of the fabric layers and the mechanical behaviour of the final composite material.
The fluid-structure interaction analysis at the micro-scale allowed to control the voids and resin pockets generation during the process and their position in the RVE geometry. In addition, the analysis provided the displacement of the tows in comparison with the initial architecture of the fabric. Increasing the pressure, the rotation of the tows was acceptable if the loading level was not bigger than 6 bar. Moreover, the fabric maintains its orthogonal architecture having a major compaction effect and the voids presence has its minimum.
Using the material properties, the lamination sequence, the geometry of the parts, and the specification of the autoclave curing cycle as input parameters, the HPC simulations set up in the first step proved to be able to provide the required information about the resulting part distortion and possible defects in the finished part in a very short amount of time. This HPC-backed simulation workflow now enables Manta Group to easily find the optimal parameters for the manufacturing process in a few minutes, thereby cutting down development times and minimizing the number of physical tests significantly.
Business benefits: reducing development time and costs while increasing competitiveness
- MANTA expects to reduce design costs by 50% (about €100.000 saving per year), material waste by 70% (about €60.000 saving per year), and raw materials usage by 15% (about €150.000 saving per year).
- CETMA expects the success story will lead to new R&D projects and consultancy services with an increase in its turnover of about €50.000 per year.
- CINECA aims to become MANTA’s provider of HPC resources estimating its related increased turnover to €20.000 per year and to exploit the success story to attract new customers with an additional increase of turnover of the same order.
EXCELLERAT Success Story
During the Excellerat P1, the success story “PC Technologies into the Computational Fluid Dynamics Software CODA” was developed and presents how the software named CODA was successfully optimised and helps to benefit further research in the aerospace industry such as simulation of aircraft aerodynamics with shorter time to solution, simulation of aircraft aerodynamics with higher resolution and higher-quality results and readiness for current and future HPC systems including hardware accelerators. Learn more about the success story here.