HPC for industry: driving innovation in Manufacturing
High-performance computing (HPC) enables companies operating in any industrial sector to become more innovative, more productive and maintain a competitive edge. But above all, with the help of cutting-edge technologies such as cloud supercomputing, artificial intelligence, machine learning and big data analysis, companies can develop products and services with a higher added value. Moreover, HPC paves the way to novel industrial applications. Embracing HPC in industry to fulfil the demands for processing highly complex tasks and large volumes of data in real-time could result in significant business benefits such as reducing costs for product or service development, considerable human resources costs savings, speed up the development process and decrease time to market. Furthermore, supercomputers can process vast amounts of data in a short amount of time, allowing companies to analyse large datasets and make better-informed decisions quickly. This can lead to improved efficiency and productivity in various aspects of a business, including manufacturing, logistics, and customer service. Advanced technologies such as AI, machine learning, and HPDA can help companies discover new patterns, trends, and insights in their data that may have been otherwise difficult or impossible to identify. This can lead to new product and service innovations, as well as improved processes and strategies.
As the supercomputers can process data with a high degree of accuracy and precision, reducing the risk of errors and improving the quality of decision-making. By leveraging supercomputers and advanced technologies, companies can optimise their processes which results in cost savings. Additionally, AI and machine learning can help companies identify cost-saving opportunities and optimise pricing strategies.
Overall, the benefits of using supercomputers and advanced technologies for business are numerous. Companies that leverage supercomputers and advanced technologies can gain a competitive advantage over their peers by making faster and more informed decisions, innovating faster, and delivering better products and services to customers, improving business efficiency, innovation, accuracy, cost savings, and competitive advantage.
FF4EuroHPC is an H2020 R&D project which promotes using HPC and complementary technologies such as HPDA and AI. Two Open Calls were offered through the project, targeting the highest quality experiments involving innovative, agile SMEs from varied application domains. SMEs were part of the experiments, that met the Open Call standards and have been carried out on the Cloud-based HPC systems. The experiment is an end-user-relevant case study demonstrating the use of Cloud-based HPC and the benefits it brings to the value chain from the end-user to the HPC-infrastructure provider thus must address SME business challenges by using HPC and complementary technologies such as HPDA and AI. When the experiment is successfully concluded, it is resulting in a success story, inspiring the Industrial community.
One of the success stories is briefly presented in this article. Please find more success stories on the FF4EuroHPC website.
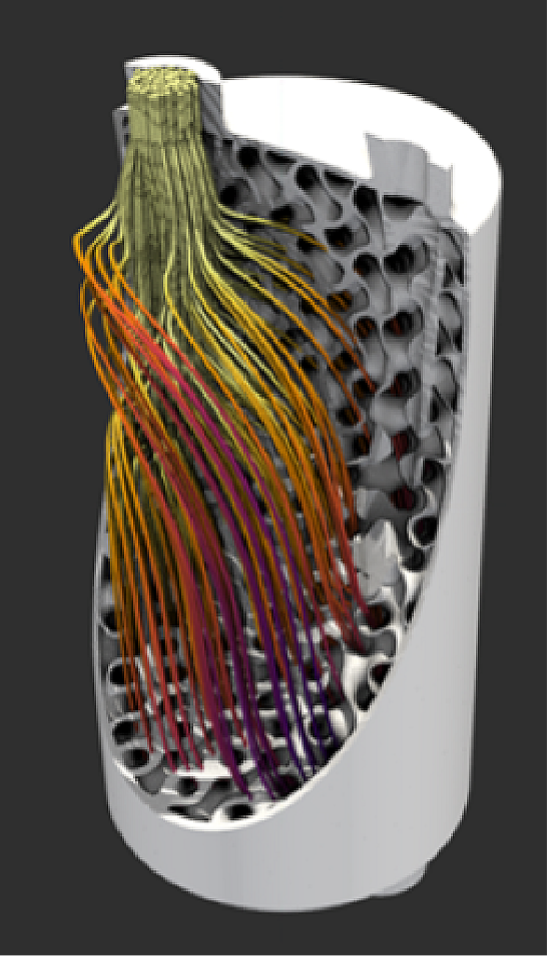
Manufacturing: Topology Optimization of Micro-Channel Heat Exchangers
Micro Channel Heat Exchanger (MCHX) are heat exchangers in which the fluid flows in lateral confinements with dimensions of millimetres. Thanks to high specific properties, efficient flow distribution and lightweight, they are gaining popularity in several industrial fields, including aerospace, bioengineering, electronics, and oil & gas.
The challenge: developing an advanced design methodology to generate innovative configurations of Micro Channel Heat Exchangers
Performances of MCHX are strongly affected by the design (shape and topology) of micro-channels. Design approaches based on experimental campaigns require many iterations, resulting in significant R&D costs and large time-to-market. In practice, due to budget and time constraints, only a few configurations are assessed, leading to sub-optimal solutions. On the other hand, a simulation-centric design approach poses several challenges including modelling, Software integration, and robustness. In addition, due to inherent multiscale nature of the problem, Conjugate Heat Transfer (CHT) simulations of MCHX require high-resolution computational models to well-resolve the fluid-dynamics at the smallest space-time scale of microchannels. Consequently, the costs associated with these computations limit severely an exhaustive exploration of the design space. Optimization is a peak requirement for a computing infrastructure. In-house HPC solutions are usually under-sized for these tasks, especially for small and medium sized enterprises. As a consequence, shortcuts must be taken to cope with the limited computational resources (e.g. the space of feasible designs is limited a priori in a heuristic manner, simplified models are developed ad-hoc for a single use case, etc.) resulting in entropic workflows, further increase of R&D costs, and ultimately affects the competitiveness on the market. Thus, the use of parallel computing becomes imperative to maintain development times compatible with industrial turnovers.
Topology optimization (TO) is an advanced design methodology to generate innovative configurations that are difficult to obtain with conventional design techniques. The complex shapes resulting from TO cannot be easily manufactured by traditional techniques such as Computer Numerical Control machining, injection moulding or vacuum casting. The Technology Readiness Level (TRL) of Additive Manufacturing (AM), e.g. laser-sintering, has boosted over the last decade, making this technology a cornerstone for new business models in the manufacturing industry. AM has several advantages such as faster production cycle, flexible design, and opens possibilities precluded to traditional manufacturing technologies, as it allows to realize components with complex geometries with relatively contained costs. A very promising application is therefore to combine both TO and AM for MCHX design. Despite the enormous potential, MCHX manufacturers are prevented from exploiting the freedom provided by the paradigm TO+AM due to the above-mentioned difficulties.
The solution: TOLOMHE framework for topology optimization
TOLOMHE is an High Performance Computing (HPC)-centric platform developed for topology optimization of MCHX. By combining advanced optimization, simulation, machine learning and deployment on a HPC infrastructure, TOLOMHE platform aims to i) increase the competitiveness of MCHX manufacturers by providing a cost-effective design tool for MCHXs, and to ii) validate an innovative business model for the independent software vendor based on the “Optimization-as-a-Service” paradigm.
The building blocks of TOLOMHE are a solver-agnostic optimizer (modeFRONTIER), a multiscale multi-physics solver for Conjugate Heat Transfer (CHT) simulation (immerFLOW), and a software for geometry manipulation (mimic). modeFRONTIER (ESTECO) is an industry-leading tool for multi-disciplinary design optimization. immerFlow (Optimad) is a high-productivity CFD solver based on an immersed boundary paradigm, particularly well-suited for automated workflows with complex geometries. Mimic (Optimad) is a tool for computer aided geometry manipulation featuring topology parametrization of implicit geometries. The multiscale nature of the fluid-dynamic / thermal coupling in MCHX is addressed through a machine learning (ML) model. The resulting approach is characterized by three nested mathematical / numerical models.
- Micro-scale model. The microscale model consists of a deep neural network which estimates local permeability and heat transfer coefficients from the (local) channel topology and flow conditions. The (synthetic) dataset used for the offline training was created on a HPC cluster (Galileo100, infrastructure of CINECA with 528 computing node, each of them with 2 CPU Intel CascadeLake 8260, with 24 core each). Each data point corresponds to high-resolution simulation performed on a single cell of “prototype” lattice topologies.
- Macro-scale model is used to simulate the flow field at the macroscopic scale for a given layout of the heat-exchanger. The effect of the microscale is incorporated in terms of local permeability and heat-exchange coefficients. These are computed by means of cheap feed-forward evaluations of the ML model. Consequently, the computational cost of a simulation for the entire heat-exchanger is drastically reduced.
- Evolutionary optimization framework is used to explore the entire design space and improve the initial design. Genetic algorithms require a large number of model evaluations during the initial exploration of the design space (from few hundreds to several thousand depending on the specific problem). To achieve this exploration in an acceptable timeframe, the optimization is performed on the HPC infrastructure, thus leveraging the high scalability of genetic algorithms. Moreover, genetic algorithms are well-suited for multi-objective and multi-constrained optimization. Within modeFRONTIER, a hybrid strategy combining Sequential Quadratic Programming (SQP) and the Non-Dominated Sorting Genetic Algorithm (NSGA-II) was selected as the optimization algorithm.
During the topology optimization the design of the MCHX is described implicitly in terms of level set function to avoid expensive (and error-prone) remeshing loops. At the end of the optimization, an explicit representation of the overall heat exchanger geometry is returned to the user in terms of a surface tessellation as provided by mimic.
Business benefits and impact of TOLOMHE
TOLOMHE value proposition revolves around three main concepts:
- It has been deployed on the HPC infrastructure thus it grants access to adequate computing infrastructure.
- No prior knowledge was required for using HPC or optimization. This helps to remove the entry barrier for first time HPC users.
- All the required tools are integrated into a single platform. This solution can remove all the issues related to integration of different (CAE/CAD) tools and licensing.
Thanks to the adoption of TOLOMHE, the end-user is expected to accelerate the transition from a build-to-print to a build-to-spec business model by reducing R&D costs and time-to-market for new products.